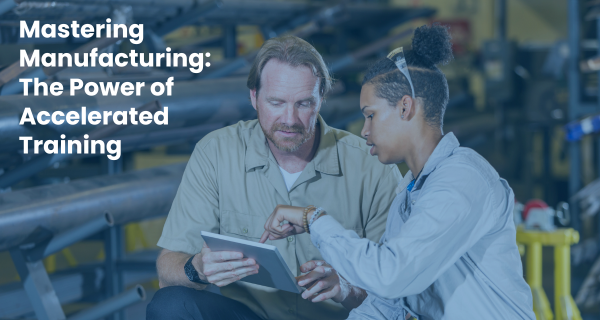
Explore how accelerated training programs can revolutionize the manufacturing industry by swiftly bridging the skills gap and elevating workforce productivity.
Summary of Key Points
- Urgency and Importance: With 65% of manufacturers facing challenges in attracting and retaining talent, accelerated training is essential for addressing this critical issue.
- Skills Gap Projection: The industry anticipates a shortfall of 2.1 million skilled workers by 2030, making rapid upskilling of new hires vital for sustained production and innovation.
- Strategic Imperative: Accelerated training is not just a response to the skills gap but a strategic necessity to prevent severe production disruptions, increased operational costs, and a decline in competitive edge.
- Effective Programs: Key components of successful accelerated training programs include targeted, role-specific knowledge, engaging delivery methods, and the use of smart forms and intuitive mobile platforms.
- Overcoming Challenges: Implementation hurdles such as resistance to change and limited resources can be overcome by fostering a culture of continuous learning and securing leadership buy-in.
- Future Trends: The future of manufacturing training includes immersive experiences like augmented reality simulations and the integration of AI and machine learning for predictive upskilling, ensuring the workforce remains agile and responsive.
The Urgency of Accelerated Training in Manufacturing
In an era where 65% of manufacturers cite the challenge of attracting and retaining talent as their primary concern, the urgency for effective solutions is at an all-time high. Accelerated training in manufacturing is not just a response to this pressing need; it’s a strategic imperative. As the industry confronts a potential shortfall of 2.1 million skilled workers by 2030, the ability to quickly transform new hires into proficient contributors is critical for sustained production and innovation.
Dan Bergner, Founder and Chief Product Officer of Youreka, emphasizes the potential impact if the skills gap remains unaddressed: severe disruptions in service, increased operational costs, and a decline in competitive edge. Accelerated training is the linchpin for manufacturers to maintain market share, meet deadlines, and ensure service quality.
Key Components of Effective Accelerated Training Programs
Effective accelerated training programs in manufacturing are characterized by their ability to deliver targeted, role-specific knowledge in an engaging and efficient manner. These programs leverage smart forms and intuitive mobile platforms, like those provided by Youreka, to furnish on-demand, personalized training modules that cater to the unique needs of each employee.
Core components include a blend of theoretical learning and practical application, real-time assessments to gauge progress, and feedback mechanisms that allow for continuous improvement in the training process. The outcome is a workforce that is not only quickly upskilled but also adaptable to evolving manufacturing technologies and processes.
Overcoming Common Challenges in Accelerated Training Implementation
The road to implementing accelerated training programs is not without its hurdles. Organizations often face resistance to change, limited resources, and the challenge of integrating new technologies with existing systems. To overcome these obstacles, manufacturers must foster a culture that values continuous learning and innovation.
Moreover, leadership buy-in and a clear communication strategy are essential to ensure that the adoption of tools like Youreka’s guided mobile forms is seamless and well-received by the workforce. Continuous evaluation and refinement of the training content will also ensure that the programs remain relevant and effective.
In previous case studies with Youreka customers, our forms, procedures, and checklists are adopted easily by employees. Shell implemented Youreka forms for 200 employees. All 200 new users required no training hours to start using Youreka.
Youreka offers guided procedures that help train employees, resulting in better efficiency and accuracy. To ensure compliance with various UK regulations, Metro Safety’s Risk Assessors now visit sites armed with a set of questions and clear guidelines. These questions range from simple black-and-white answers to more complex ones with multiple options, depending on the answers to the preceding questions.
Future Trends in Manufacturing Training and Workforce Development
Looking ahead, the manufacturing sector is poised to see an even greater emphasis on accelerated training as a cornerstone of workforce development. Trends indicate a shift toward more immersive training experiences, such as augmented reality simulations, that can further compress the learning curve and prepare employees for complex tasks in a risk-free environment.
Additionally, the integration of artificial intelligence and machine learning into training programs will enable predictive upskilling, where training needs are anticipated and addressed proactively. This proactive approach to employee development will be critical for manufacturers to remain agile and responsive to the rapid changes in the industry.
Ready for Solutions to Your Training and Upskilling Hurdles?
If you’re ready to talk about your training needs, contact us with your questions at letstalk@youreka.io.